The machine comprises four major components, a sturdy bridge supported on two steel columns within which is mounted the diamond wire drives and cooling system. The diamond wire spans the space between the two vertical columns and can be raised or lowered under controlled conditions. Beneath the main structure the fourth item comprises a sturdy support bed mounted upon rails to allow any object to be moved under close control between the vertical columns when required to undertake the horizontal cutting. This carriage will be provided with bespoke clamping features to remotely secure items for cutting and attached to the carriage there s a steel beam that is used to support the sections as they are being cut away.
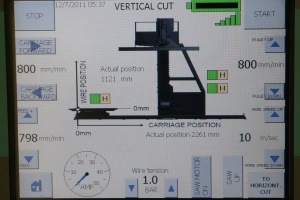
The Stealth incorporates the latest developments in wire technology such that the nature and specification of the diamond cutting beads are matched to the demands emanating from the object to be cut such that maximum cutting efficiency is delivered. The scale of the demonstration machine as currently configured - 4.7m high, 4.5m wide and with a horizontal bed movement of up to 20m - will allow it to undertake sectioning of items of substantial size. These dimensions are flexible and can be adjusted to suit specific requirements.
The whole ethos of The Stealth lies in the very high quality of the components utilised, the skill in developing diamond wire to suit a range of duties and the bespoke software that enables the operator to undertake specific actions under very closely controlled conditions. Throughout the cutting process the machine monitors key functions such as the wire velocity, wire tension, the main carriage and support carriage velocities and the power amperage in the main wire drive motor. This is dry, cold cutting and one vital feature of the machine is the presence of a bespoke module in the main head to cool the wire continuously during operations. The software is also capable of undertaking repetitive operations of a batch nature with minimal supervision.
The Stealth can take difficult areas of nuclear decommissioning to a new plane, where highly active and contaminated items can be remotely size reduced under closely controlled conditions. The control to cut in different planes without recourse to material realignment is a major step forward and has the potential to significantly reduce the volume of many decommissioned items ahead of their disposal.
We would be pleased to demonstrate the capabilities of the STEALTH to potential clients and to discuss their practical needs which may be met by their use of a bespoke machine designed around their specific requirements.